In a groundbreaking leap in 3D printing technology, scientists at ETH Zürich have introduced a remarkably human-like robotic hand. This innovative creation mimics the composition of a human hand, incorporating bones, ligaments, and tendons. The key differentiator is the use of various flexible polymers to emulate the building blocks of a human skeleton, showcasing the vast potential applications of this cutting-edge technology.
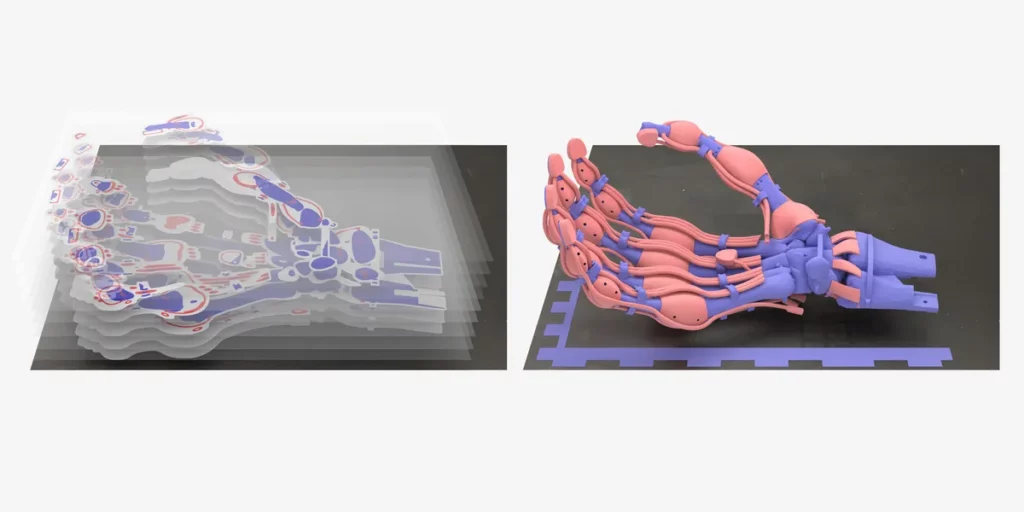
In the not-so-distant past, the idea of having 3D printers in our homes seemed like a far-fetched sci-fi concept. Yet, the rapid evolution of 3D printing technology has turned this fantasy into reality. From printing edible delights and plant-based fish alternatives to crafting medical devices and even functional rockets, the capabilities of 3D printing have expanded exponentially.
Traditionally, 3D printing was confined to fast-curing plastics, limiting the range of materials that could be utilized. However, researchers at ETH Zürich, in collaboration with US-based startup Inkbit, have pioneered new methods. These advancements now enable the incorporation of slow-curing plastics, facilitating the printing of objects with multiple materials simultaneously. The ability to combine soft, elastic, and rigid materials has unlocked the potential for more intricate and complex shapes.
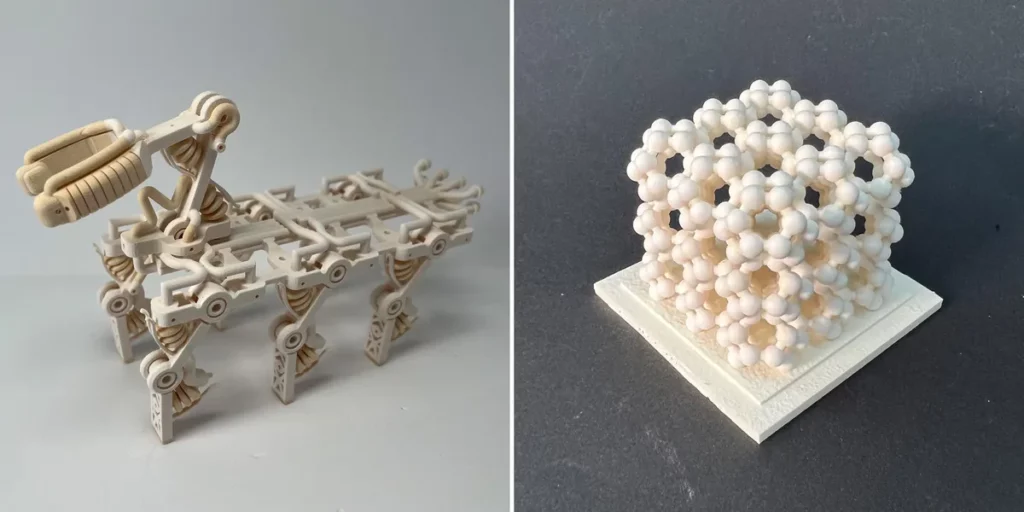
The shift to slow-curing ethylene polymers has been instrumental in achieving the lifelike robotic hand. Thomas Buchner, the first author of the study, noted, “We’re now using slow-curing ethylene polymers. These have very good elastic properties and return to their original state much faster after bending than polyacrylates.”
Typical 3D printing builds up shapes in layers, using a UV lamp to cure the plastic between each layer. However, this method is unsuitable for slow-curing plastics, as they remain sticky and could disrupt the printing process. To overcome this challenge, the team implemented laser-based 3D scanning for each layer. This process allows the machine to recalibrate and adjust for irregularities, eliminating the need to smooth the surface after each layer.
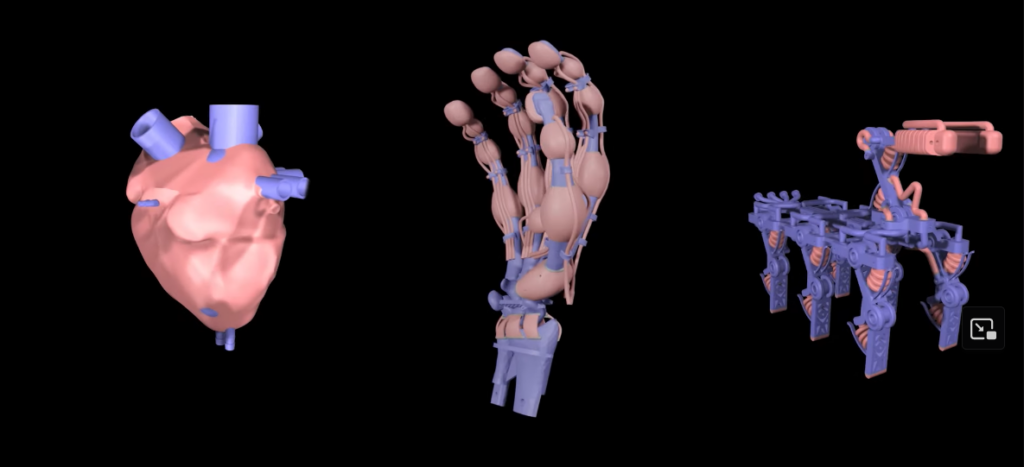
Professor Wojciech Matusik of MIT, where Inkbit is based, explained the innovative technique: “A feedback mechanism compensates for these irregularities when printing the next layer by calculating any necessary adjustments to the amount of material to be printed in real-time and with pinpoint accuracy.”
The implications of this advanced 3D printing technique extend beyond the creation of a lifelike robotic hand. The team has successfully fabricated a diverse range of high-resolution composite systems and robots, including tendon-driven hands, pneumatically actuated walking manipulators, pumps mimicking a heart, and metamaterial structures.
Senior author Professor Robert Katzschmann highlighted the advantages of robots made from soft materials, such as the 3D-printed hand. These soft robots pose a lower risk of injury when working alongside humans and are better suited to handle delicate objects.
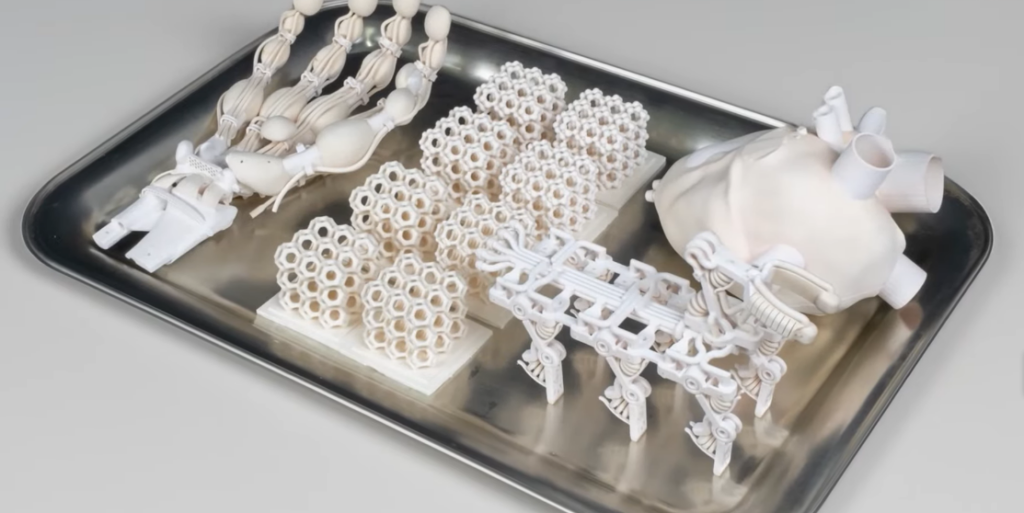
This breakthrough in rapid and versatile manufacturing technology opens new avenues for scientific investigations, experimental design, complex prototyping, and industrial innovation. The researchers envision a future where their innovative 3D printing technology continues to push the boundaries of what is possible in the realm of robotics and beyond.